What is Porosity in Welding: Essential Tips for Achieving Flawless Welds
Porosity in Welding: Identifying Common Issues and Implementing Best Practices for Avoidance
Porosity in welding is a prevalent concern that usually goes unnoticed up until it triggers significant troubles with the integrity of welds. This typical problem can endanger the strength and longevity of welded frameworks, posing security threats and resulting in pricey rework. By understanding the origin of porosity and implementing efficient avoidance approaches, welders can considerably enhance the top quality and reliability of their welds. In this discussion, we will discover the vital elements contributing to porosity development, analyze its destructive effects on weld performance, and talk about the very best techniques that can be taken on to minimize porosity occurrence in welding processes.
Typical Sources Of Porosity

Making use of dirty or damp filler products can present contaminations right into the weld, adding to porosity concerns. To minimize these usual reasons of porosity, thorough cleansing of base steels, correct securing gas option, and adherence to ideal welding criteria are necessary techniques in accomplishing top notch, porosity-free welds.
Effect of Porosity on Weld High Quality

The existence of porosity in welding can substantially jeopardize the structural honesty and mechanical residential or commercial properties of welded joints. Porosity creates gaps within the weld steel, compromising its overall toughness and load-bearing capability. These voids act as stress and anxiety focus points, making the weld more at risk to splitting and failure under used tons. Additionally, porosity can lower the weld's resistance to rust and other ecological elements, better reducing its longevity and efficiency.
One of the key consequences of porosity is a decline in the weld's ductility and toughness. Welds with high porosity degrees often tend to display reduced impact stamina and lowered ability to warp plastically prior to fracturing. This can be particularly concerning in applications where the bonded parts go through vibrant or cyclic loading problems. Porosity can restrain the weld's ability to efficiently transfer forces, leading to early weld failing and possible safety and security hazards in crucial structures. What is Porosity.
Finest Practices for Porosity Prevention
To improve the structural integrity and quality of welded joints, what specific measures can be implemented to decrease the event of porosity throughout the welding process? Porosity prevention in welding is crucial to ensure the honesty and toughness of the final weld. One effective practice appertains cleansing of the base metal, removing any kind of pollutants such as rust, oil, paint, or moisture that can result in gas entrapment. Guaranteeing that the welding equipment remains in great problem, with tidy consumables and suitable gas circulation prices, can likewise considerably lower porosity. Furthermore, maintaining a secure arc and managing the welding parameters, such as voltage, existing, and take a trip speed, assists create a regular weld swimming pool that reduces the risk of gas entrapment. Making use of the correct welding technique for the particular material being bonded, such as readjusting the welding angle and gun placement, can even more protect against porosity. Routine inspection of welds and instant removal of any concerns identified during the welding procedure are vital techniques to stop porosity and generate top quality welds.
Relevance of Correct Welding Techniques
Implementing proper welding techniques is critical in guaranteeing the structural stability and quality of welded joints, building on the foundation of effective porosity avoidance actions. Welding strategies straight affect the general stamina and sturdiness of the welded structure. One key facet of correct welding methods is preserving the appropriate heat input. Too much warmth can cause enhanced porosity due to the entrapment of gases in the weld swimming pool. Alternatively, inadequate heat might cause incomplete fusion, developing prospective powerlessness in the joint. In addition, making use of the suitable welding parameters, such as voltage, existing, and travel rate, is vital for accomplishing audio welds with very go to this site little porosity.
Moreover, the choice of welding process, whether it be MIG, TIG, or stick welding, need to align with the certain needs of the project to make sure optimum results. Appropriate cleansing and prep work of the base metal, in addition to picking the appropriate filler material, are likewise crucial components of skilled welding strategies. By sticking to these best practices, welders can lessen the threat of porosity development and produce top quality, structurally sound welds.
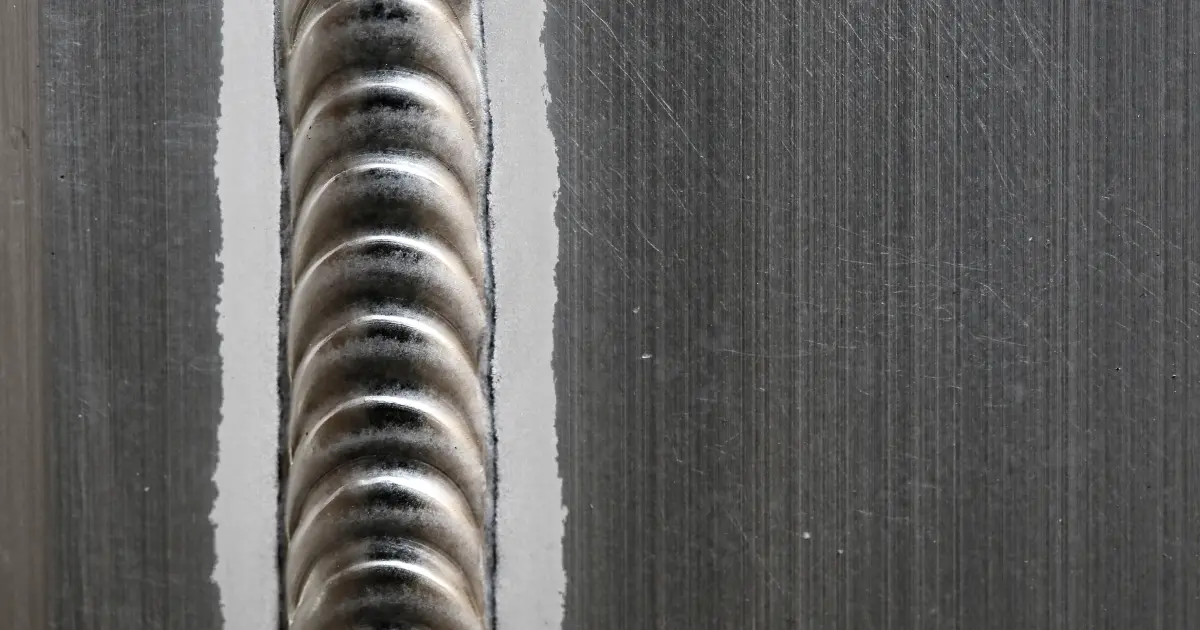
Evaluating and High Quality Control Procedures
Testing treatments are necessary to find and avoid why not try these out porosity in welding, ensuring the toughness and toughness of the final item. Non-destructive screening methods such as ultrasonic screening, radiographic testing, and aesthetic assessment are commonly used to determine possible flaws like porosity.
Post-weld assessments, on the various other hand, examine the last weld for any type of flaws, consisting of porosity, and verify that it satisfies specified standards. Executing an extensive quality control plan that consists of thorough screening treatments and assessments is vital to minimizing porosity problems and guaranteeing the overall top quality of bonded joints.
Final Thought
In final thought, porosity in welding can be a common concern that influences here are the findings the high quality of welds. By identifying the common root causes of porosity and carrying out best practices for avoidance, such as appropriate welding techniques and screening steps, welders can ensure excellent quality and trustworthy welds. It is vital to prioritize avoidance techniques to decrease the incident of porosity and maintain the honesty of welded frameworks.